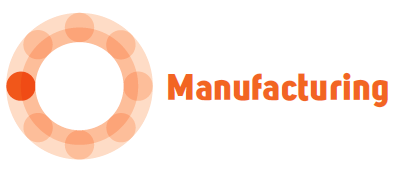
Ensuring build quality and controlling costs is essential for manufacturers. OneFit Manufacturing modules provide essential control throughout the manufacturing process. From detailed specifications and material requirements
planning (MRP) through to completion of the finished product. BOMs (Bills of Materials) hold all the necessary raw
material and production information and allow you to keep related documentation for use in production or despatch
which can also include specification test results for Quality Assurance purposes. Works Order loading can be managed
traditionally or OneFit Visual Controller can be deployed to present easy to view machine and operator assignment.
Operations and performance are monitored and can be viewed throughout your business operation supplying critical
information to dependent departments. Shop floor data capture and process control can be handled with touchscreens
and manual operation or by capturing digital production data.
Works order processing
Increase productivity and fulfil orders
on time
Closely manages production
Quick and simple multiple order
creation
OneFit Visual Controller manages
overall operations or individual
production cells
Works Orders automatically
generated from Sales Orders
Route cards, operation cards and
picking lists
Multiple issues and returns to stock
allows monitoring of stock usage,
costings and traceability by batch
The ‘Backflush’ option enables users
to complete works orders by issuing
stock retrospectively
Digital or manual shop floor data
capture using either touch screen
or automatic capture if using CNC
machines
Management of production flow for
sequential operations using touch
screen technology
Operation and operator time
recording and monitoring
Works orders can be traced through
the factory via touchsceen terminals
Immediate onscreen display of
supporting documentation, images,
drawings, production guidelines and
COSHH at the production area or cell
Works Order Planning/Scheduling
Traditional Planning
OneFit Visual Controller provides
graphical stacked planning and
scheduling tools
Graphical monitoring of real time
machine and operator assignments
Materials Requirement Planning(MRP)
Calculates and forecasts material
and production requirements using
sales order demand, current stock
levels, existing purchase and works
orders to a specified date
Calculate and run material plans
for all demands accommodating
supplier and production lead times
Provides a JIT purchasing/planning
model to reduce working capital
for stock
displayed to assist in the decision
process
Provides a JIT purchasing/planning
model to reduce working capital for
stock
Bill of materials
Simple and logical to set up
specifications for the control of
manufactured items including any
required components, operations
and associated documentation
Comprehensive management of
your product assemblies
Unlimited numbers of nested levels
of sub-assemblies
Up to date re-costing to provide
accurate information for production,
materials and labour costs
Define maximum batch size and
machine load limitations
Image and document storage
against each BOM e.g. COSHH, user
manuals, works order instruction,
product documentation and
specification tests